Plywood plays a crucial role in the construction industry, particularly in the creation of durable curved concrete forms. These forms are essential for achieving unique architectural designs and structural integrity in various building projects. Understanding the properties of plywood, the science behind curved concrete forms, and the challenges and solutions associated with using plywood for concrete forms is vital for successful construction. Additionally, exploring the future trends in plywood and concrete forming can provide insights into potential advancements and innovations in this field.
Understanding Plywood and Its Properties
Plywood is a versatile material commonly used in construction due to its desirable characteristics. It consists of multiple layers (or plies) of thin wood veneers, bonded together with strong adhesive. This composition gives plywood its strength, stability, and resistance to warping or shrinking. The thickness and type of wood veneers used determine the specific properties of the plywood.
Another challenge faced when using plywood curved concrete forms is the risk of delamination due to prolonged exposure to moisture and chemicals present in the concrete. Delamination can weaken the plywood sheets, compromising the stability of the formwork and posing safety hazards on the construction site.
One advantage of plywood is its ability to withstand the pressure exerted by wet concrete, allowing it to function as a formwork material for casting concrete in desired shapes. Plywood also exhibits good dimensional stability, meaning it remains relatively unchanged in size and shape even when subjected to moisture or temperature variations.
The Composition of Plywood
Plywood consists of an odd number of layers, typically three or more, with each layer having its grain direction rotated by 90 degrees. This cross-grain arrangement enhances the overall strength and stability of the plywood. Additionally, the use of high-quality adhesives contributes to the structural integrity of the material.
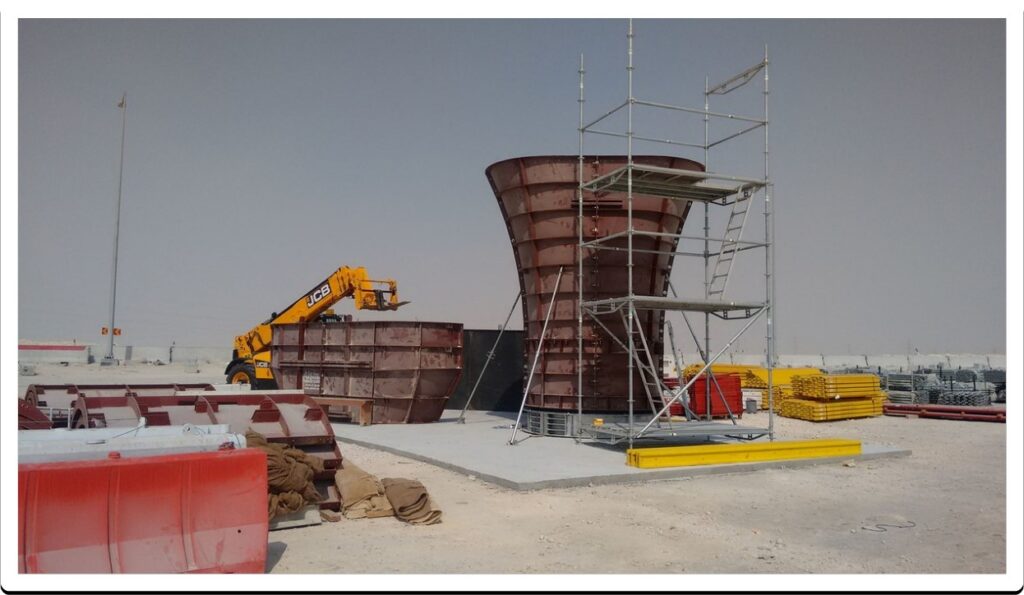
Why Plywood is Preferred for Construction
There are several reasons why plywood is preferred over other materials for construction purposes. Firstly, plywood is readily available and cost-effective, making it a practical choice for construction projects of various scales. Secondly, plywood has high load-bearing capacity, enabling it to support the weight of wet concrete during the casting process. Additionally, plywood is easy to work with, allowing for customization and flexibility in creating curved concrete forms.
Moreover, plywood offers excellent durability, making it suitable for long-term use in construction projects. Its resistance to decay and insect infestation ensures that structures built with plywood will stand the test of time. Furthermore, plywood is a sustainable choice, as it is made from renewable resources and can be recycled at the end of its life cycle.
Another advantage of plywood is its versatility in design. It can be easily cut, shaped, and molded into various forms, making it ideal for creating intricate architectural details. Whether it’s for decorative purposes or functional elements, plywood offers endless possibilities for creative expression in construction.
The Science Behind Curved Concrete Forms
Creating curved concrete forms involves a scientific approach that combines structural engineering principles with material selection. The process aims to achieve desired architectural aesthetics while ensuring the durability and safety of the structure.
Read more at: Exploring the Advantages of Concrete Plywood in Formwork Construction
The Process of Creating Curved Concrete Forms
The process of creating curved concrete forms begins with careful planning and design. Architects and engineers collaborate to determine the desired curvature and the structural requirements of the formwork. This collaboration ensures that the formwork not only meets the aesthetic goals but also provides the necessary strength and stability to support the weight of the concrete.
Once the design is finalized, plywood is cut and shaped according to the specified curves and dimensions. This step requires precision and attention to detail, as even the slightest error in the formwork can lead to significant issues later on. Architects and engineers use advanced computer software to aid in the design and fabrication process, ensuring accuracy and efficiency.
Next, the plywood pieces are securely fastened together to form the desired shape. It is crucial to ensure tight joints and reinforcements to prevent leakage of concrete and maintain the form’s integrity during the pouring process. The use of steel reinforcements and bracing is common in curved concrete forms, as they provide additional strength and stability.
After the formwork is constructed, it is coated with appropriate release agents to facilitate easy removal once the concrete has cured. This step is essential to maintain the desired shape and surface finish of the architectural element. The choice of release agent depends on various factors, including the type of formwork material and the desired surface texture of the concrete. Find more about element at https://www.chem.purdue.edu/gchelp/atoms/elements.html
Factors Affecting the Durability of Concrete Forms
The durability of concrete forms is influenced by various factors. One significant factor is the quality and selection of the formwork material. Plywood’s resistance to moisture and dimensional stability are crucial in ensuring the longevity of the forms. Architects and engineers carefully choose the type and grade of plywood to withstand the pressure exerted by the concrete and to resist warping or swelling due to moisture exposure.
Additionally, factors such as concrete mixture proportions, curing methods, and environmental conditions can impact the overall durability and lifespan of the concrete forms. The concrete mixture must be properly proportioned to ensure adequate strength and durability. Curing methods, such as moist curing or the use of curing compounds, play a vital role in preventing cracking and enhancing the concrete’s long-term performance.
Furthermore, environmental conditions, such as temperature and humidity, can affect the curing process and the overall durability of the concrete forms. Extreme temperatures or high humidity levels can lead to rapid drying or prolonged curing times, potentially compromising the integrity of the forms. Architects and engineers consider these factors during the planning and construction stages to ensure the longevity and performance of the curved concrete forms.
Plywood’s Role in Concrete Forming
Plywood plays a vital role in the strength and stability of concrete forms. Its unique properties make it an ideal material for constructing formwork that can withstand the weight and pressure exerted by wet concrete. The use of plywood in concrete forming offers numerous benefits for construction projects.
When considering the role of plywood in concrete forming, it is essential to understand the specific characteristics that make it a preferred choice for builders and contractors. Plywood is known for its high strength-to-weight ratio, which means it can support heavy loads without adding unnecessary bulk to the formwork. This strength is crucial during the concrete pouring process, where the formwork must bear the weight of the liquid concrete without buckling or deforming.
How Plywood Contributes to the Strength of Concrete Forms
Plywood acts as a supportive structure to hold the concrete in place until it cures and gains sufficient strength. Its robust nature prevents deformation or collapse during the pouring and curing stages. Plywood’s load-bearing capacity allows for the creation of large and complex curved forms without compromising their strength or stability.
Moreover, plywood offers dimensional stability, ensuring that the concrete form maintains its shape and integrity throughout the curing process. This stability is crucial for achieving precise and accurate concrete structures, especially in architectural projects that demand high levels of detail and accuracy. To read more about stability click here.
The Benefits of Using Plywood in Concrete Forming
Using plywood in concrete forming offers several advantages. Firstly, plywood is readily available and cost-effective compared to alternatives such as metal or fiberglass formwork. Secondly, plywood can be easily cut and shaped to achieve intricate shapes and curves, allowing for creative architectural designs.
Plywood also provides a smooth surface finish to the cast concrete, minimizing the need for additional surface treatments or finishes. Additionally, plywood is reusable, reducing waste and improving sustainability in construction projects.
Overall, the use of plywood in concrete forming not only enhances the structural integrity of the concrete but also offers practical and economic benefits to construction projects of all scales. Its versatility, strength, and cost-effectiveness make plywood a valuable material in the world of concrete construction.
Challenges and Solutions in Using Plywood for Concrete Forms
While plywood is an excellent choice for concrete forms, certain challenges may arise during its usage. Understanding these challenges and implementing innovative solutions can help overcome potential issues and ensure successful construction projects.
When it comes to using plywood for concrete forms, it is crucial to consider the environmental conditions on the construction site. Extreme temperatures and high humidity levels can impact the performance of plywood, affecting its dimensional stability and durability. Proper storage of plywood panels in a dry and well-ventilated area can help prevent moisture absorption and maintain the integrity of the formwork.
Common Issues in Using Plywood for Concrete Forms
One common issue is the potential for plywood to absorb moisture from the concrete mixture, leading to dimensional changes and warping. This can result in inaccuracies in formwork and affect the quality of the final concrete structure. Additionally, repeated use of plywood may cause wear and tear, reducing its structural integrity over time.
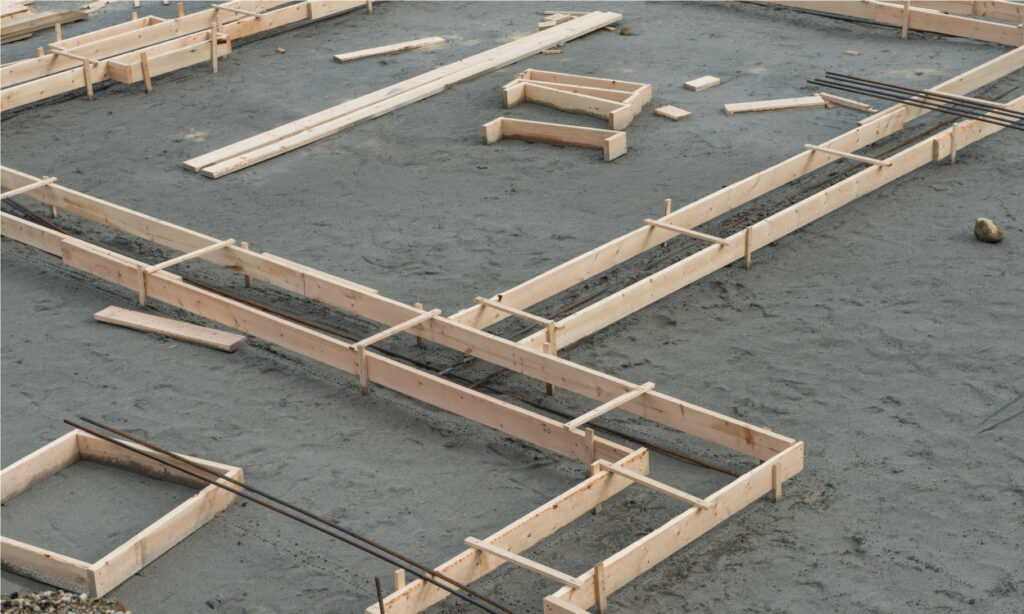
Innovative Solutions to Overcome Plywood-Related Challenges
Several innovative solutions address the challenges associated with using plywood for concrete forms. Applying appropriate coatings or sealants to the plywood surface can protect it from moisture absorption and prolong its lifespan. Using moisture-resistant plywood or treating the plywood with waterproofing agents can also mitigate moisture-related issues.
Furthermore, implementing proper formwork release agents can enhance the ease of demoulding and minimize the risk of damage to the plywood. Regular inspection, maintenance, and timely replacement of worn-out plywood panels contribute to the overall efficiency and longevity of the formwork.
By staying informed about the potential challenges and adopting proactive measures, construction professionals can optimize the use of plywood for concrete forms, ensuring the success and durability of their projects.
Future Trends in Plywood and Concrete Forming
The future of plywood and concrete forming holds potential for exciting advancements and technologies that can revolutionize the construction industry. Technological innovations in plywood manufacturing and the exploration of new materials are likely to shape the future of curved concrete forms.
Technological Advancements in Plywood Manufacturing
Continuous research and development in plywood manufacturing techniques can lead to the production of even stronger and more resilient plywood. Advanced bonding methods and the use of sustainable materials in plywood production contribute to its enhanced performance and environmental friendliness.
The Future of Curved Concrete Forms with Plywood
As architects and designers continue to push the boundaries of architectural aesthetics, curved concrete forms using plywood are expected to gain further popularity. The combination of computer-aided design and manufacturing technologies with the versatility of plywood will open up new possibilities for creating complex and innovative curved structures.
Moreover, the integration of smart materials and advanced formwork systems can optimize the efficiency and cost-effectiveness of constructing curved concrete forms. By leveraging technological advancements and sustainable practices, plywood’s role in creating durable and aesthetically appealing curved concrete forms is set to evolve in the future.